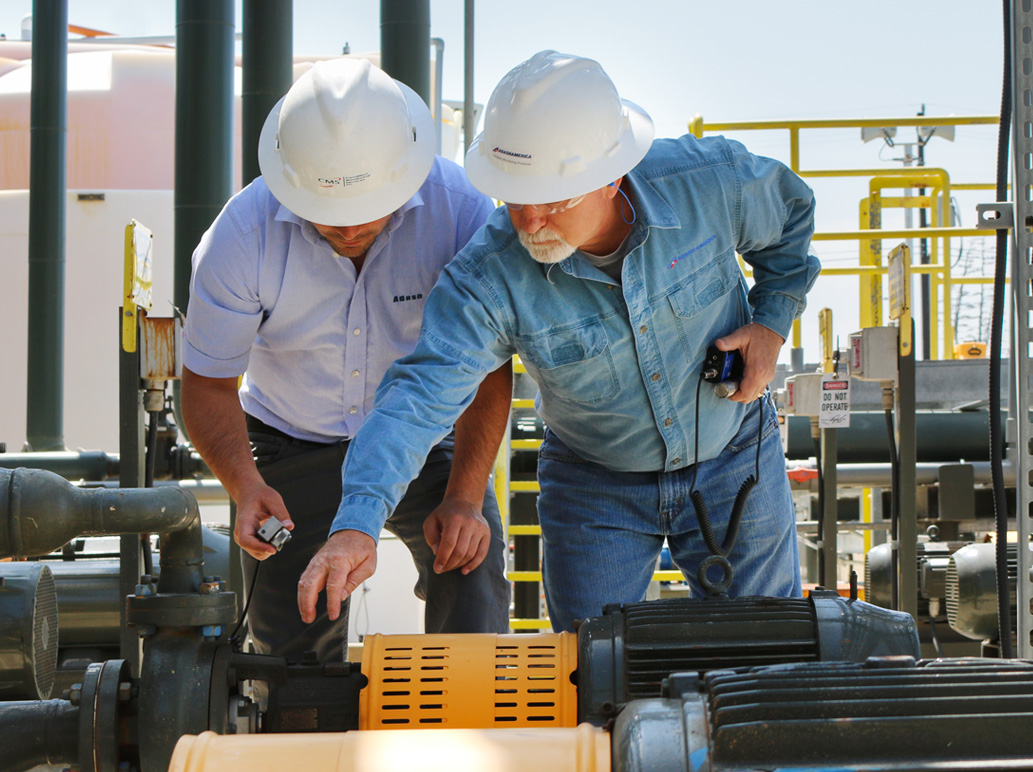
Predictive Maintenance 4.0 Knowledge (Maintworld magazine)
When I visit maintenance conferences these days, I hear quite a lot about predictive maintenance (with an explanation of what it is), much less about vibration diagnostics (usually with the comment that it is too difficult to explain and that nobody would
AS THERE ARE no standards for Industry 4.0, almost everything can be related to it. So the companies are competing over who will have more labels stating “Industry 4.0” on their products or in advertisements, even though – in many cases – there is hardly anything really revolutionary. The maintenance world has focused heavily on Predictive Maintenance lately. This simply means that a machine should not be repaired after it fails, nor too early when it is still in good condition. The machine should be repaired when it is really needed. The right moment is when failure is near – or in other words when the fault starts affecting the machine, but it is still safe to keep the machine running until the time for repair suits the company best (for example during a planned shutdown).
It is commonly recognized that the factory that uses a predictive maintenance programme is ready for Industry 4.0 and fulfils Industry 4.0 visions. The main section of Predictive Maintenance is Vibration Diagnostics, which can quite precisely detect machine condition from the vibration signal; actually the vibration diagnostics cannot detect it on its own, but the vibration specialist who understands measured values and graphs can do that. There is one problem: there are still more and more machines to be maintained and fewer specialists who understand vibration diagnostics (and this is a fact that has been confirmed by many universities already).
As a result of this, vibration analysts are harder to find and therefore they are
also becoming more expensive to hire. Why do we actually need such expertise to evaluate vibration data? You may think that the diagnostics system in a car is of a higher level because the driver who does not understand how the engine works can easily understand what the diagnostics system is telling him or her (ie. change the brake pads, change the rear bulb, stop vehicle – engine lubrication failure). It is easy for a basically trained mechanic to understand complicated faults with a good diagnostics system. It is because a modern vehicle is usually overloaded with various sensors and control electronics (that can, however, sometimes be counter-productive - from my own experience) and can be far from what predictive maintenance should be. This is rather preventative maintenance. On the other hand, a technician in a factory is usually equipped with only one vibration sensor and data collector (and he can be happy to have even those) so he has to rely on his knowledge and experience.
Situations like this are luckily a thing of the past. There is vibration diagnostics equipment on the market that can evaluate overall machine condition and find the source of a developing failure. All this can be done without any special knowledge required from the technician operating the device. This fact actually is, I dare to say, truly Industry 4.0 revolutionary - the system evaluates the data, not the vibration expert.
The system algorithm was developed based on the long-term experience of Adash vibration diagnostics experts. It is called the Expert System or Faults Source Identification Tool (FASIT). The FASIT system algorithm mostly uses data from FFT analysis and evaluates it as a vibration expert would do. The outcome of this evaluation is an easy to understand graph showing the severity and type of the developing fault. The outcome can be saved in professional software called DDS so the trend of fault severity is recorded this way. The trend of fault severity is much easier to understand than the trend of vibration values, which can be numbers understandable only for a vibration specialist. There is no need for a vibration expert for evaluation when the outcome says, for example, Severity of Unbalance 80 percent and you can see it is in the red bar.
This way we can avoid a frequent management dilemma, which is: “We need to start vibration diagnostics, but who will do that? Nobody here understands it really.” The solution for this is very easy: contact an Adash distributor on the website www.adash.com and get a predictive maintenance solution suitable for your factory. Once it is done, you just need to collect the data and follow the instructions generated by the FASIT Expert System. In this way the picture of machine condition can be quite clear. There is only one new concern: what to do with all the saved money that would normally be spent on unexpected shutdowns, a vibration expert’s salary or a service company?
Industry progress is heading toward sophisticated automatization even in areas where it was hardly imaginable a few years ago. It is not heading there because it was planned that way, but it is heading there because of market demands and modern technologies that are now available. Industry 4.0 actually popularizes and names continuous technology development. I believe that this popularization will lead to a bigger interest in technical studies for young people and that vibration diagnostics and predictive maintenance will be understood as the principle of a successful company, not as an unpleasant costs item involved in bookkeeping.