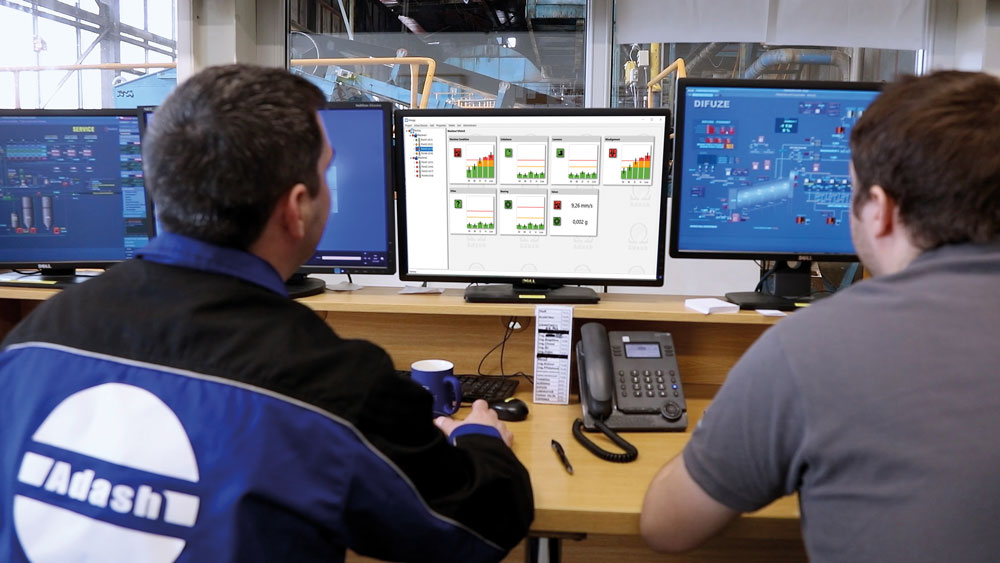
How to Monitor Critical Machines?
Adash has launched new software for fault monitoring. In the development phase, AI did not bring significant benefits. The analytical software is based on industry experience.
Some machines need to be monitored 24/7. For such situations remote online monitoring systems are standard solutions these days. The word ‘remote’ can have many meanings, but in all of them you do not physically stand next to the machine. The machine is equipped with sensors and the values are measured by a unit connected to the sensors.
In one case, the values can be displayed in the control room. However, not all the monitored data is easily readable by the maintenance staff in the control room. For example, temperature and pressure are easily understood by everyone, but what about vibration values? What is 6 mm/s? Is it a low or a high value? Should the machine be stopped? Do I call an expert? What do I do with all the numbers I have in the control room? Do I need to hire a vibration expert to check these values? If the vibration expert is going to analyse the data occasionally, it's not really 24/7 monitoring, is it?
Another option for remote monitoring is to store the values in the cloud, where an analyst checks the data on a regular basis. In this case, the vibration expert is involved in the scenario, but that's not 24/7 monitoring either. It also needs to be decided which vibration expert to hire. You can hire a vibration expert who can go out in the field and get to know the machines first, which is certainly the right choice. Or you can hire a team of diagnosticians who are remote and may be cheaper, but they may be so far away that they can't visit the field (if they've ever been to any machinery park).
The ideal situation would be for a vibration expert to monitor the measured values continuously, but that is not possible in the real world. At Adash, we have been trying to solve this problem for years. We have been looking for a way to help maintenance staff find machine faults without the constant presence of a vibration diagnostics expert.
WE TALK DIRECTLY TO OUR CUSTOMERS
New features in Adash products are developed according to customer requirements. We are in direct contact with our customers all the time. You can call our office and speak directly with an expert. There is no administrative wall between our customers and the Adash office. As a result, we always have a list of customer requirements of what they lack in the field of vibration diagnostics. One of the recurring requests was for an online monitoring system with a feature that automatically detects machine faults.
10 years ago, we developed an expert system called FASIT (Fault Source Identification Tool) that shows machine faults and their severity. The FASIT system is designed exclusively for Adash portable vibration meter and analyzers. It means you have to physically stand next to the machine to find faults. However, the big step was to enable maintenance staff who have no knowledge of vibration diagnostics to do so. Without any knowledge of spectra, frequency bands or other terms, maintenance personnel could see directly from the screen of the portable analyser, for example: an unbalance has been detected, its severity is high and balancing is necessary. This was the first step towards something bigger. A few months ago we launched our new Online Monitoring Expert Guard Application (Omega for short).
Simply put, Omega is an expert system that gives you information about the major problems with your machines and their severity. If you don't have a vibration diagnostics department, Omega gives you a great way to get information about the condition of your machines. It can also be a great help for your diagnostic teams. It really does monitor your machines 24/7.
OMEGA IS ANALYTICAL SOFTWARE, NOT ARTIFICIAL INTELLIGENCE!
Omega is analytical software based on industry experience. The creators of the software have many years of experience in vibration measurement and analysis.
Omega software is not an artificial intelligence system. We have tried to use AI several times in the past, but we have found and empirically verified that it is not possible. There is a very simple reason for this. There are thousands of different machines with dozens of possible faults. There is no way to get sufficient training data. To put it simply, it can be compared to medicine. There are AI attempts to diagnose patients medically, and they are still not reliable enough. In this case, there is only one type of organism - the human body (in terms of machines - only one type of machine). And now let's imagine that there is an AI that reliably diagnoses humans and all animals. You can see that this is not possible.
HOW DOES IT WORK AND WHAT IS NEEDED TO USE IT?
How exactly does the Omega software work and what does it take to use it? It has 2 parts. The first part is the software in the online monitoring unit (Adash A3716 or Adash A3800). You need to install the accelerometers on the machine. In the basic machine setup, there is one acceleration sensor mounted radially per bearing and one acceleration sensor mounted axially on the machine. If the speed is variable, you also need a speed sensor. Faults and their severity are identified directly in the A3716/A3800 unit. The information is placed on Adash's OPC server, where it can be displayed, for example, on the control room screen.
The second part is the software installed on the computer. You set up a measument tree with its measurement points and displays the measurement results and the Omega analysis. The Omega software automatically determines the measurements to be taken.
Simply put, Omega is an expert system that gives you information about the major problems with your machines and their severity.
The result is a traffic light-coloured graph showing the machine's faults and their degree of severity. You can use Adash Omega's graphical user interface for this, but it can also be displayed using third-party software you already use (in which case the data must be taken from Adash's OPC server).
WHICH FAULTS CAN BE DETECTED IN THIS WAY?
As we run the system, the trend curves start to fill in. The trend curves show the severity of the faults. The severities are basically calculated according to the thresholds defined in ISO 20816 part 3. The user can change the thresholds if necessary. The graphs are displayed in traffic light colours, which makes them easy to read for the user. There are no numbers to confuse the user, only the machine faults and a colour bar indicating their status.
The following faults are displayed: unbalance, misalignment, looseness and bearing condition. You can see if these faults have been detected on the machine by using the traffic light colours. Green means that the fault is insignificant, orange means that you should be alert to the possible development of the fault, and red means that the severity of the fault is high. The trend graphs show the evolution of the severity of the fault. You can see the current value, but also the average value of the last hour, last day, last week and last month. Each bar also has a vertical black line showing the maximum and minimum values measured over that period. This shows whether the measured values have been stable or not.
VIBRATION EXPERTS ALWAYS HAVE THEIR PLACE
There is also one graph with a question mark icon. This graph is for situations where there is something wrong with the machine, but Omega doesn't know exactly what it is. In this case, you should call a vibration expert. You may be wondering, do I still need a vibration expert at the end of the day? Yes, of course! You always do! But with Omega software, the need for a vibration expert is greatly reduced. The importance of a human vibration expert can never be beaten by even the best analysis software. But the software must be developed to greatly assist the vibration expert and maintenance personnel, which was Adash's goal.
The Omega software has been on the market for a short time and we are now eagerly awaiting feedback from users around the world. We have carried out the first beta project in several companies and the results look promising. If you too are joining the world of Omega users, we look forward to your comments. Your comments are of immeasurable value to us.
What is the result of this? Physical presence can never be fully replaced by remote analysis. The software cannot see splashing oil or hear strange noises coming from a machine. However, remote diagnostics plays an important role in today's maintenance.